Laser has been a buzzword of the future since the acronym was coined in 1959, and ray guns have been a staple of science fiction since the late 1800s. Today, that fanciful concept has matured and been harnessed to advance industry. How did Lasers go from Buck Rogers to making bucks, and how can something that blew up a planet in Star Wars or nearly cut James Bond in half be utilized safely in a production facility like yours? The reality of modern lasers may not be as exciting as their media portrayal, but they are significantly safer if used correctly.
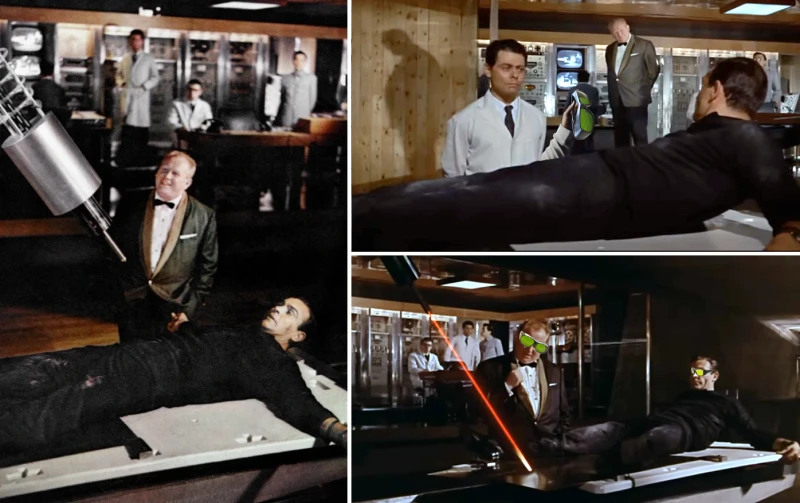
Laser is an acronym: Light Amplification by Stimulated Emission of Radiation
The difference between laser devices and conventional, omnidirectional light sources is that lasers generate a stimulated emission via photonic chain reaction rather than light being a byproduct of thermal activity. This allows for a coherent, collimated (single direction), monochromatic (single wavelength) beam emission that can travel great distances without dispersion, being applied with extreme precision, and/or being put to work changing the physical characteristics of an object. While omnidirectional light sources can be collimated by means of lens or parabolic reflector, the energy transfer potential is not anywhere near the output of a laser. Long story short: Lasers allow us to put light to work.
So how did lasers grow from fanciful science theory into a mature, useful technology relevant to flexography and packaging?
Industrial use of lasers first emerged in the 1960s with applications in distance sensors and cutting tasks. Advances in laser design, construction, and precision and allowed for laser printing on paper in the 1970s and a huge technological leap forward in the 1980s; lasers allowing instantaneous communication over distance, widespread and common laser cutting, engraving, and the laser engraved ceramic anilox roll all contributed to revolutionizing the packaging industry. Lasers continued to be increasingly utilized in the 1990s, introducing the computer-to-plate and laser die cutting processes. With their literal light-speed operation, Lasers enable a high-speed replacement of many formerly low-speed physical contact based tasks. Due to their speed and efficiency lasers often require significantly less energy than the tasks and mechanisms they replaced.
After decades of technological advancement and cost reduction lasers have become ubiquitous in modern life including the packaging industry. The trend for widespread use of lasers was recognized as early as 1968 when ANSI (Z136) set out to define safety for this growing technological field, with OSHA (29-CFR 1910, PUB 8-1.7) and the FDA (21-CFR 1040) following closely behind in the 1970s. Over a thousand pages of regulations simply put: safe use of lasers centers around managing, minimizing, or eliminating human exposure to them. Lasers are separated into categories, called classes, based on risk of injury.
These four classes have several sub-classes, but the general notion of each category is as follows:
- Class 1 – Fully enclosed or embedded, no risk of human exposure to laser radiation.
Example: Blue ray movie player.
- Class 2 – The laser is in the visible light spectrum and not enclosed, but eyes are protected by the aversion response and is incapable of causing damage unless viewed with collecting optics (binoculars, for example). The aversion response is a natural reflex to blink or look away from an unpleasant excess of light radiation entering the eyes.
Example: bar code scanners.
- Class 3 – The laser is in the visible light spectrum and not enclosed. Eye injury is possible, but unlikely unless viewed directly.
Example: laser pointers (3R), 3D printers and light shows (3B)
- Class 4 – The laser is not enclosed, is likely outside of the visible light spectrum preventing an aversion response, is a hazard to eyes or skin from both specular (mirror) and diffused reflection, may pose a fire hazard, and may also produce airborne gas/particle hazards.
Example: cutting and cleaning lasers.
Increasing Safety
As the hazards increase, the controls and procedures necessary for safe use also increase. Most lasers used to cut, clean, or engrave will be class 4 and occasionally 3B operating as class 1 through the use of protective enclosures. A class 1 enclosure not only keeps operators safe, it removes the requirement inherent in class 3B and 4 lasers to have a laser controlled area, a Laser Safety Officer (LSO) present during use, and many other extra safety measures.
Class 4 lasers are capable of generating light emission pulses vastly brighter than the surface of the sun, and even with a few hundred watts of output can travel several kilometers before dispersing enough to be within safe levels. Even the indirect, reflected emissions can be significant enough to require notifying the Federal Aviation Administration in some cases of unguarded operation due to a multi-kilometer hazard bubble. The eye injury danger can be instantaneous as a single direct laser pulse can cause explosive boiling of the eye’s internal fluid and many industrial lasers work outside of the human visible light spectrum, eliminating protection opportunity via the aversion response that helps prevent eye injuries from looking at the sun too long, for example. Often unnoticed at the time of injury, cumulative degradation can also be incurred from diffused surface reflections or other indirect exposure to high power lasers.
A common frequency range for industrial lasers is the near-infrared band (IR-A), 750 to 1400 nanometer wavelength. The chart below illustrates potential injuries for unguarded high-power lasers within this band.
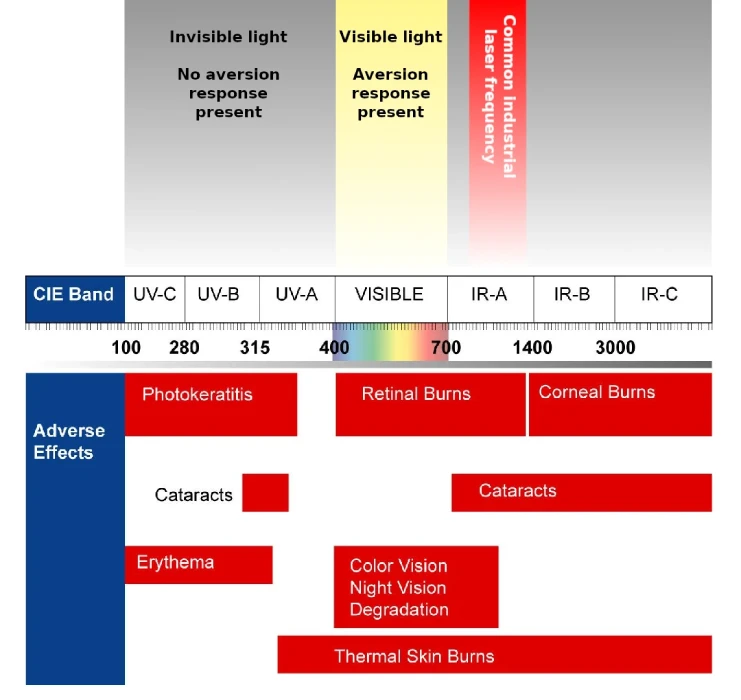
A prime example of this risk is unguarded lasers used for cleaning press equipment in print facilities, often in-press; there are 19 OSHA violations in these 4 roll cleaning photos alone:
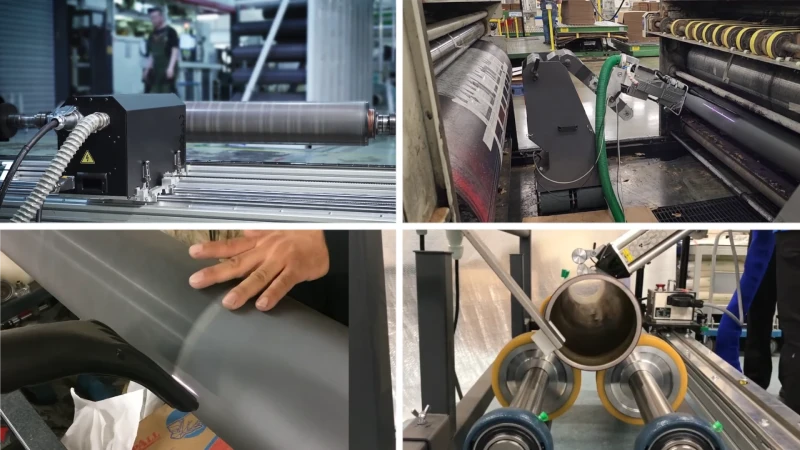
While there are other safe methods of in-press roll cleaning, lasers are best used off-press contained inside a class 1 enclosure. Along with the inherent safety benefits, roll cleaning inside the enclosure allows the high precision tolerances and controlled movement that allows lasers to clean a roll without damage. There is a risk of excessive dwell time causing etching when a laser needs to adjust to the press movement due to press driveline speed tolerances, chain bounce, inconsistent movement, vibration, or unplanned motion stoppage. Additional to that risk is the surrounding press components; ignition of greases, damaging plastic tubing, hot work permits, building beam stops, establishing a safety perimeter that could stop production for equipment neighboring the press, and any enclosed area permits that may be necessary with that perimeter.
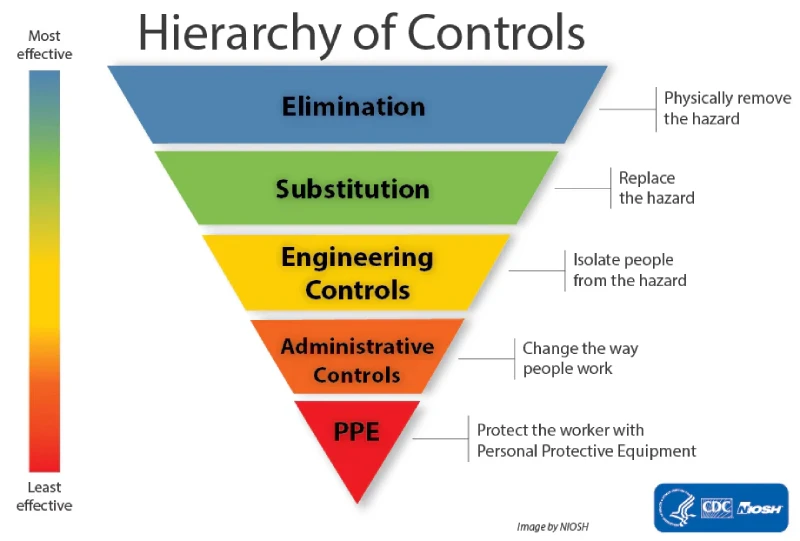
Referencing the NOISH hierarchy of controls diagram, the class 1 enclosure satisfies both substitution and engineering controls when compared to open, unguarded use of class 3 and class 4 lasers. Class 1 enclosures inherently satisfy both the intent and letter of all applicable U.S. laser safety standards by completely isolating the hazards inside, making high power industrial lasers no more dangerous than your Blu-ray disc player at home.
Safe and routine use of lasers has accelerated the evolution and growth of our industry. Understanding laser safety can be a complex, moving target but the overall premise remains consistent: keep the operator away from exposure to open high powered lasers. This is similar to other industrial safety practices such as keeping fingers away from pinch points, but differs in that the point of hazard interaction may be invisible to your operators. Most reputable laser vendors and contractors will utilize enclosures to achieve this goal; speaking with their Laser Safety Officer during the sales interaction and asking what safety measures are in place is a prudent and crucial part of the decision making process.
For further information, please reference